01 Common
Wood flour is ground wood with a particle size of less than 1.2 mm. The production of wood flour is governed by GOST 16361-87 “Wood flour. Technical Specifications”, according to which this product is divided into grades (120, 140, 160, 180, 200, T, 250, 560, 1250) according to size and quality parameters and application:
- 120, 160 – production of light-colored phenolic plastics
- 140, 180 – production of phenolic plastics, industrial explosives, polymer composite and building materials
- 200 – production of alkyd linoleum, building materials, starch molasses production
- 250 – production of industrial explosives
- T – production of pigmented titanium dioxide
- 560, 1250 – production of filter elements and catalysts
Existing wood flour production lines include three main stages: pre-drying, grinding and classification. Drying is one of the most energy-intensive stages. Grinding is carried out in hammer crushers, which produce a small amount of product in small fractions, less than 200 microns. Existing wood flour production lines involve preliminary drying before grinding. This stage is the most energy-consuming. A partial solution to this problem is to combine grinding and drying in a mill using the heat generated during grinding. And the presence of the mill’s boundary separation allows to obtain a product of a given particle size distribution. The vertical shaft impactor mill MC-640 with the help of the elements of boundary separation allows to obtain the smallest fractions of wood flour of narrow
02 Raw material
Waste from woodworking production was used as a feedstock:
wood chips with a maximum size of 40 mm

sawdust
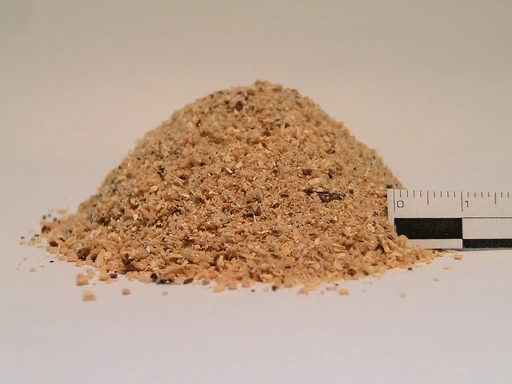
The moisture content of the raw material is 20%.
03 Grinding
The input raw materials were ground at different mill settings.
When the mill was set to maximum capacity:
Capacity – 150 kg/h
Sieve analysis:
0-400µm – 40%.
>400µm – 60%.
When the mill is set to maximum grinding:
Capacity – 50 kg/h
Sieve analysis:
0-40µm – 56%
40µm-160µm – 34%
160µm-400µm – 9%
400µm – 1%.
The moisture content of the raw material is up to 8%.
04 Output material
Wood flour after grinding:

05 Photo analysis
Magnification ×230
The division price is 10µm
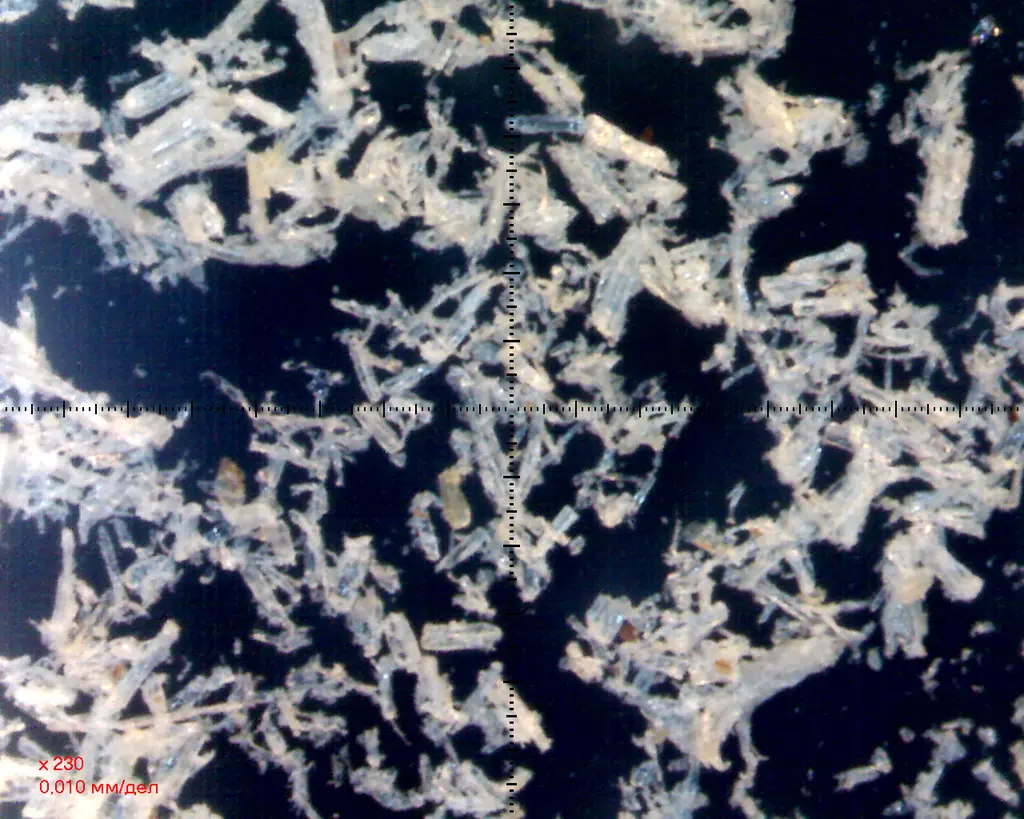
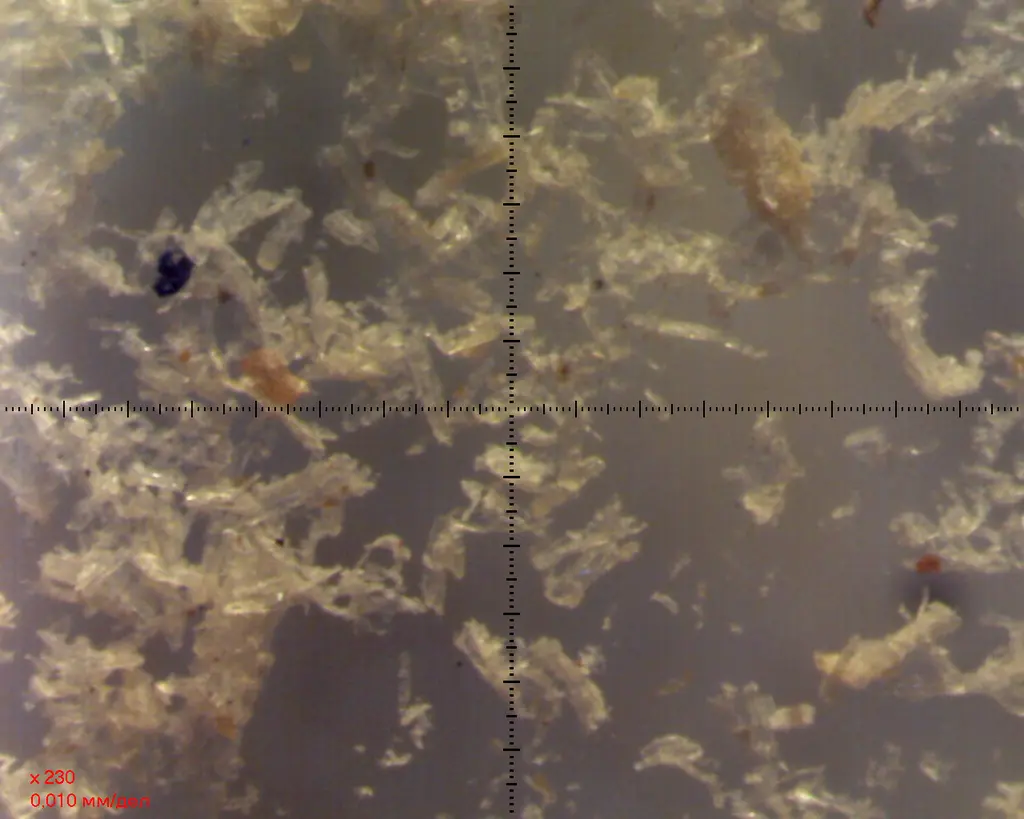
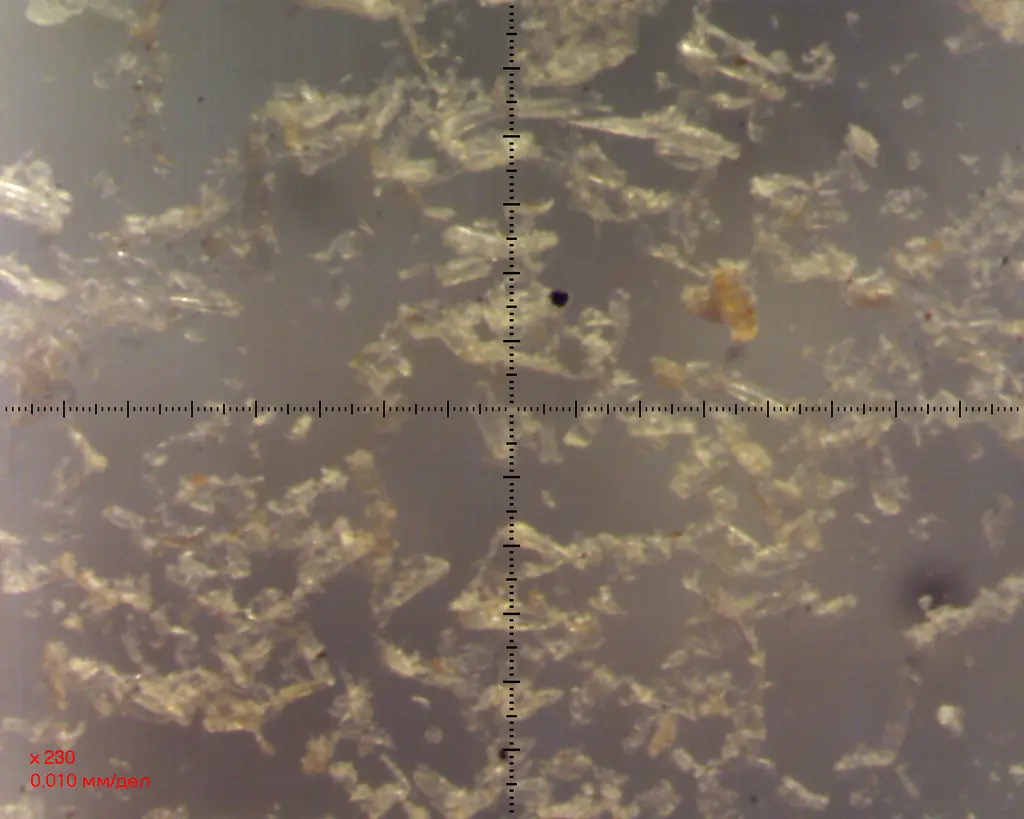
The crushed particles have a rectangular shape with an aspect ratio of 1:3-1:5.
06 Features
During grinding, the input raw material is dried.
The maximum moisture content of the feedstock is 40%.
The crushed particles retain the micro shape of the fibers.