Vertical shaft impact mill MC-640
01 Fine grinding
02 Low energy consumption
03 High-quality mixing
Technical specifications
01 Exterior view
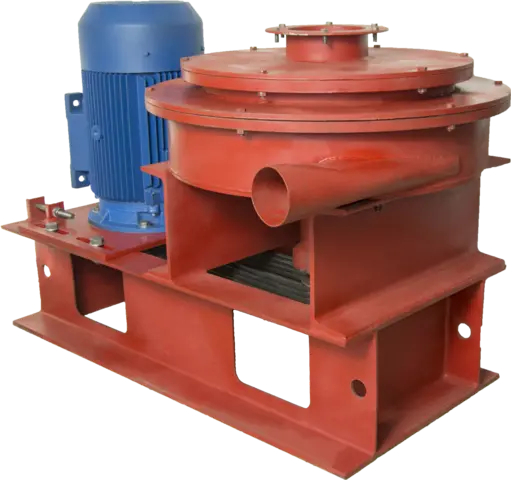
Dimensions (L×H×W) – 1,4m×1,0m×0,8m
Power – 18,5kW
Weight – 650kg
02 Industrial
equipment
for non-stop fine and ultrafine grinding of mixtures of ore and non-ore rocks; brittle, fibrous and elastic materials of low and medium hardness (up to 4.5 units on the Mohs scale).
The principle of operation is a combination of high-speed impact crushing, grinding in vortex flows and air classification.
03 Feed size
depends on the bulk density of the material.
For plant materials such as wood – up to 40mm
For rocks – up to 5mm
04 The size of
the grinding
Grinding results in a material that is not uniform in its particle size distribution.
The most straightforward method of determining the particle size distribution is sieve analysis, in which the powder is separated into sieves of different sizes.
Thus, the particle size distribution is defined in terms of discrete size ranges (fractions): for example, % of the sample between 71 microns and 80 microns when using sieves of these sizes.
The design features of the MC-640 mill allow you to adjust the maximum size of the upper fraction of the material particle size distribution.
As a result the size range of the grinded particles is from 1 micron to 200 microns.
05 Capacity
overall depends on the physical and chemical properties of the material to be ground in combination with the required particle size at the mill outlet.
So, the more restricted the upper fraction size limit is, the lower the сapacity.
The maximum capacity is:
- For rocks – 0.7 tons per hour;
- For plant material – 0.3 tons per hour.
In addition, to increase capacity, it is possible to combine several mill units into a single production line.
06 Features
The destruction of the material during the grinding process leads to the formation of grains of the correct shape (close to the shape of crystals).
For fibrous and needle-like materials, the crushed particles are not long fibers, but rectangular with an aspect ratio of 1:3-1:5.
The material dried without additional heat supply during the grinding process.
Also it allows combining grinding and high-quality mixing with small amounts (1-5%) of additives.
The use of vertical shaft impact mills requires the mandatory use of related equipment such as an air transport system with an aspiration system (bag filters, etc.).
07 Wear and tear
The working elements of the mill are made of a tungsten-cobalt hard alloy and have a strength of 86-92 HRA.
When grinding materials with a hardness of up to 2 Mohs units, the working elements are practically not subject to wear. But for materials with higher hardness, wear depends on the physical and chemical properties.
07 Price
19000$ and UP
Internal structure
01 Schematic view of the mill
in section
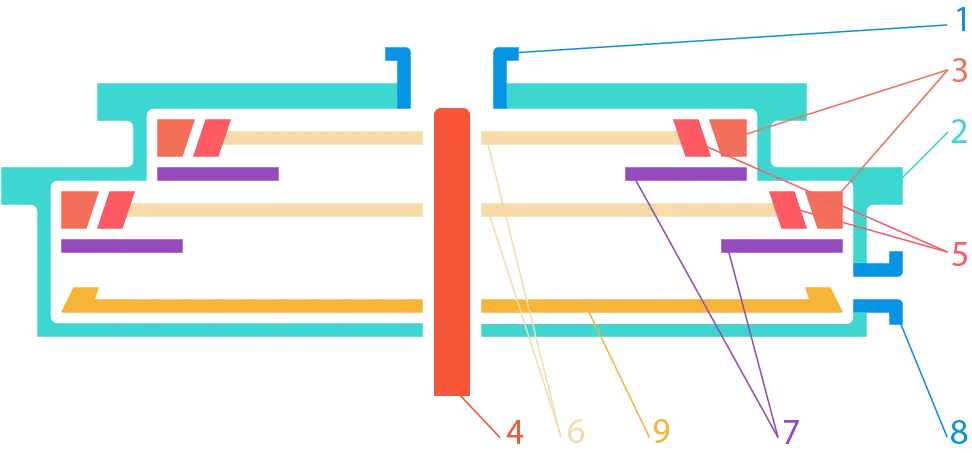
- loading nozzle
- stepped body
- baffling elements
- shaft
- beater elements
- working disks
- separation disks
- discharge nozzle
- blower
02 Principle of operation
A disk rotor is located inside the stepped body 2 on a vertical shaft 4. Each stage of the rotor is made in the form of a disk 6, which has the shape of a circle. On the disks are located the beaters 5.
On the inner side of the body 2 there are baffling elements 3. The mill chambers are separated by ring-shaped separation disks 7.
The mill operates as follows. The incoming material with air through the feed nozzle 1 enters the first stage on the disk 6 and due to the action of centrifugal forces and air flow moves to the grinding zone formed by the beater elements 5 and the baffle elements 3. Large particles are either destroyed at the moment of impact with the baffling elements 3 or return to the rotor disk 6 due to elastic forces and vortex flows.
The small particles contained in the input material and those formed in the process of its destruction pass the distance between the rotor disk 6 and the baffling elements 3 under the action of the air flow and than enter the separation zone formed by the ring-shaped separation disk 7 and the lower surface of the rotor disk 6.
Further the particles entering the separation channel are subjected to centrifugal and aerodynamic forces opposite to each other. If the centrifugal force acting on the particle is greater than the aerodynamic force, the particle returns to the intensive grinding zone, and if vice versa, it enters the next grinding stage, where the grinding and separation process described above is repeated at higher loading speeds.
As a result the ground product, along with the air flow, is removed from the grinding chamber through the discharge nozzle 8.
Technological line of grinding
01 General
The MC-640 mill easily integrated with existing grinding lines.
If you do not have an existing line, we will consider several options.
The technological line uses standard equipment, but with consideration of the physical and mechanical properties of the material to be ground:
- To ensure that the material does not hang in the hoppers, it is necessary to consider both the dynamic and static collapse angles.
- Feeders can be either sluice or screw type. The choice also depends on the material properties;
- Diameters of the connecting pipelines calculated taking into account the density of the particles and their velocity;
- The brand and size of the filter surface selected depending on the material and its particle size distribution;
- Brand and diameter of a cyclone are chosen based on the characteristics of the material it is handling and air flow.
We provide all these parameters necessary for the selection of related equipment when purchasing a mill.
02 Recommended option
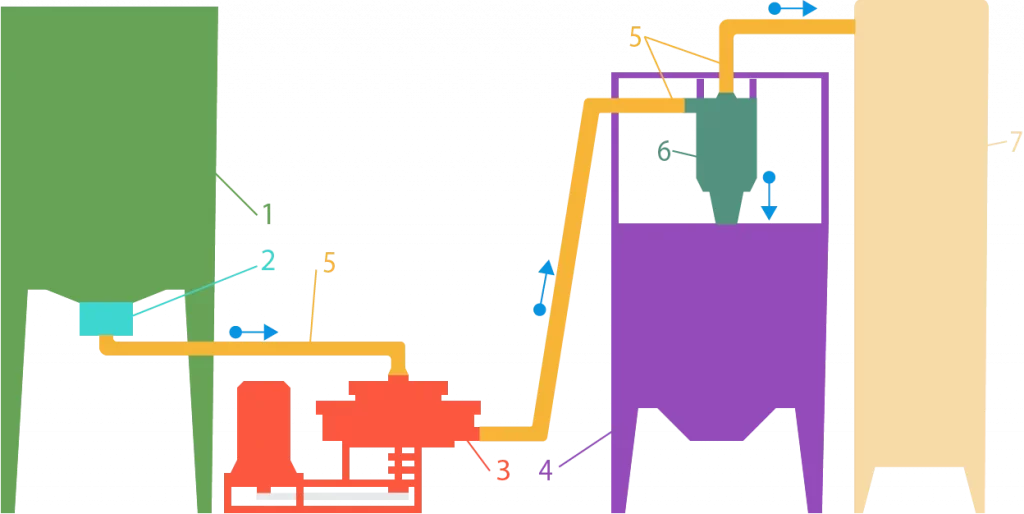
- hopper for incoming materialу
- sluice feeder
- mill MC-640
- hopper for crushed material
- air transportation system
- cyclone
- aspiration system (bag filter, etc.)
03 Minimal option
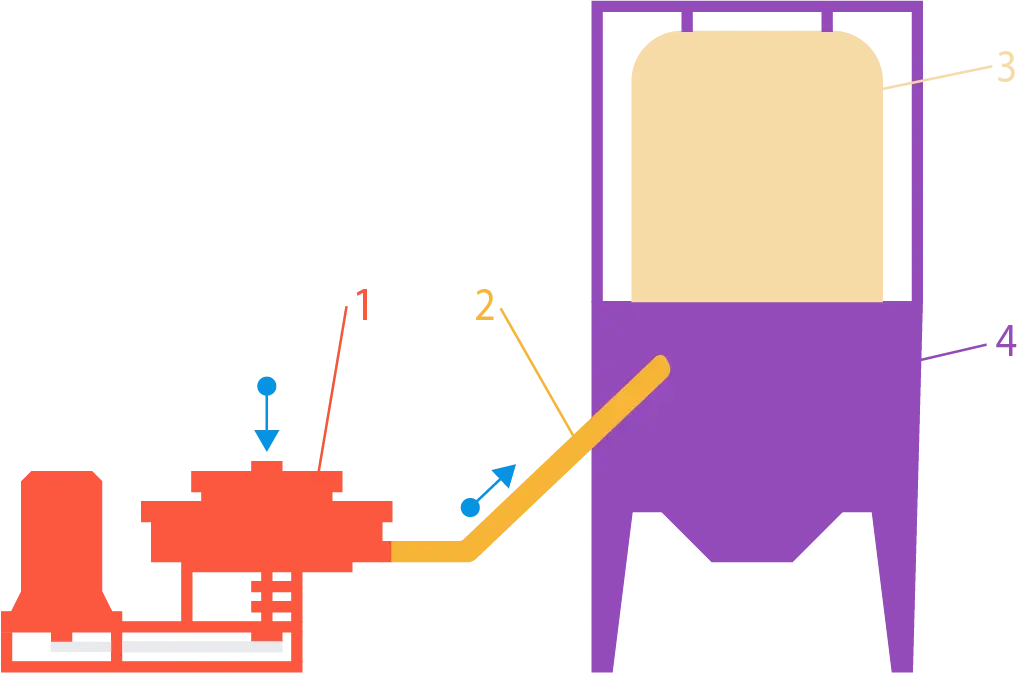
- mill MC-640
- air transportation system
- aspiration system
- hopper for crushed material
Main areas of application
01 Construction
Grinding of micro calcite (chalk, gypsum, marble)
Production of cements, dry building mixes, fillers for paints and varnishes
02 Mining
Processing of rocks and ore concentrates
03 Agriculture
Production of fertilizers, feed, plant protection products, etc.
04 Other
Production of pigments from mineral raw materials
Processing of industrial waste (slag, thermal power plant dumps, etc.)
Co-grinding, mixing of components (hydrophobized chalk, etc.)
How to buy a mill?
01 Contact us
in any way convenient for you from those listed on the site
What will we ask you?
- What kind of material do you need to grind?
- Physical and chemical properties (Mohs hardness; moisture content; particle size at the inlet, etc.)
- What particle size distribution do you want to get after grinding?
- Permissible residue on the sieve (Sieve analysis)
- Required productivity?
- etc.
02 Sample grinding
If our technical specialist confirms that it is possible to perform a sample grinding, than we will perform it free of charge for a small amount of material (up to 10-15 kg).
Because this amount is enough to analyze the particle size distribution of the grinded material.
We have the ability to perform sieve analysis or photo analysis.
You can also perform a more accurate analysis yourself using laser diffraction or any other method you need.
We grind only in your presence.
03 Purchase
Only upon successful results of a sample grinding test to your and our satisfaction.
The purchase price includes:
- mill MC-640
- instruction/training of your technical specialist
- operation
- scheduled maintenance
- calculation of air filters for your material
- recommendations on the organization of the technological line
- drawings of wearing parts (working elements)